Comprehending the Secret Components and Fixing Approaches for Packaging Machine Upkeep
Efficient maintenance of product packaging devices hinges on an extensive understanding of their essential parts, including the frame, drive system, and securing systems. Acknowledging typical maintenance concerns, combined with the execution of preventative methods and troubleshooting strategies, can considerably enhance maker reliability. Furthermore, the option of repair techniques, including making use of OEM parts and the value of certified professionals, plays a vital role in lessening downtime. To truly comprehend the details of these systems and their maintenance, one have to consider the more comprehensive ramifications of neglecting these necessary techniques.
Secret Components of Packaging Equipments
Packaging devices are composed of several vital components that collaborate to make certain efficient and reliable packaging processes. At the core of these devices is the framework, which provides architectural honesty and houses the numerous operating components. The drive system, commonly a mix of gears and motors, promotes the activity of elements, allowing accurate operation throughout the product packaging cycle.
An additional necessary element is the conveyor system, which carries products through various phases of the packaging process. This is usually enhanced by sensing units and controls that keep track of the position and rate of things, making certain synchronization and lessening errors. The filling system is essential for properly dispensing the best quantity of item into packages, whether in fluid, powder, or strong type.
Securing systems, including heat sealants or adhesive applicators, play an essential function in securing plans, stopping contamination and prolonging service life. In addition, classifying systems are essential for providing essential product information, making sure compliance with laws. The control panel, furnished with user-friendly interfaces, permits drivers to manage maker functions, screen performance, and make adjustments as needed, guaranteeing ideal performance and efficiency in product packaging operations.
Typical Maintenance Concerns
Effective operation of product packaging equipments relies heavily on routine upkeep to stop usual concerns that can interfere with production. Among these problems, mechanical deterioration prevails, particularly in components like seals, conveyors, and electric motors, which can bring about unexpected downtimes. Additionally, misalignment of parts can lead to ineffective procedure, triggering items to be inaccurately packaged or harmed throughout the process.
Another typical maintenance problem includes the build-up of dirt and particles, which can disrupt the equipment's sensing units and relocating parts. packaging machine repair service. This not only impacts efficiency but can likewise present security threats. Lubrication failures can lead to raised rubbing, resulting in getting too hot and ultimate component failure.
Electrical troubles, often stemming from loosened links or worn-out electrical wiring, can disrupt machinery functions, leading to considerable production delays. Software program glitches due to inappropriate setups or outdated programs can impede the device's procedure, requiring prompt intervention. Addressing these typical upkeep concerns proactively is vital for ensuring optimum performance and durability of packaging machinery.
Preventative Upkeep Methods
Executing preventative upkeep techniques is critical for sustaining the performance and reliability of product packaging machines. These methods incorporate a methodical approach to maintenance, concentrating on the routine evaluation and maintenance of devices to preempt possible failures. By adhering to a set up maintenance program, drivers can identify damage on components before they bring about significant failures.
Crucial element of visit their website a preventative upkeep technique consist of regular evaluations, part, lubrication, and cleaning replacements based upon manufacturer recommendations. Using lists can enhance this procedure, ensuring that no vital jobs are forgotten. In addition, maintaining accurate records of upkeep tasks help navigate to this site in tracking the machine's performance gradually, facilitating notified decision-making relating to future upkeep demands.
Educating team on the importance of preventative maintenance improves conformity and cultivates a society of positive care. Executing a predictive maintenance part, making use of information analytics and sensor technology, can further maximize equipment efficiency by anticipating failures prior to they take place.
Troubleshooting Techniques
When confronted with malfunctions or inadequacies in packaging machines, using methodical troubleshooting techniques is crucial for determining and dealing with concerns quickly. The primary step in effective troubleshooting is to develop a clear understanding of the device's functional parameters and efficiency metrics. This involves assessing the maker's specifications, in addition to any error codes or alerts displayed.
Following, operators must carry out an aesthetic evaluation, looking for apparent signs of damages, wear, or misalignment. This commonly includes checking out sensing units, gears, and belts to determine prospective root causes of malfunction. Gathering functional information, such imp source as production prices and downtime logs, can additionally offer understandings right into recurring problems.
As soon as potential issues are determined, making use of a logical method to separate the root reason is essential. This might call for testing private components or systems in a regulated manner. Taking part in discussions with drivers who communicate with the machinery routinely can produce beneficial responses concerning uncommon behaviors or patterns.
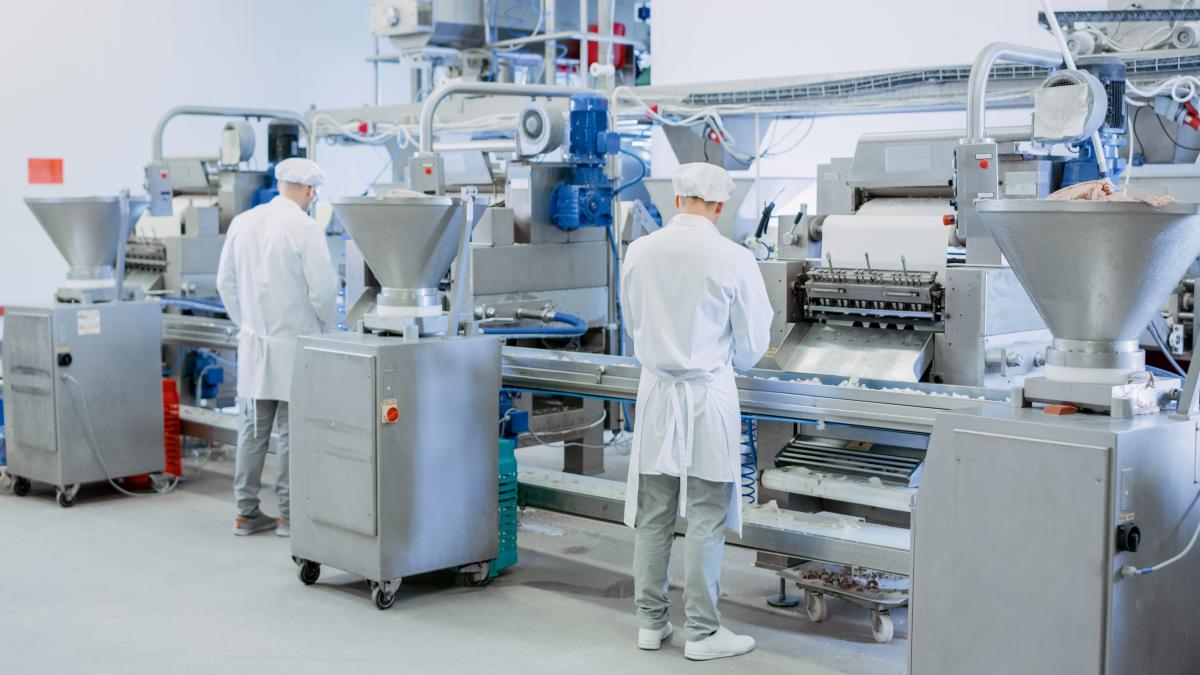
Repair Service and Substitute Finest Practices
A thorough understanding of fixing and replacement ideal methods is vital for preserving the longevity and efficiency of packaging equipments. On a regular basis evaluating the problem of machine elements enables timely intervention, avoiding even more significant issues that can cause costly downtimes.
When repair work are necessary, it is vital to utilize OEM (Original Tools Maker) parts to make certain compatibility and performance. This not only protects the honesty of the device but likewise maintains warranty contracts. Furthermore, it is advisable to maintain an inventory of important extra components to facilitate quick substitutes and lessen operational interruptions.
For complicated repair work, involving qualified professionals with specialized training in packaging machinery is recommended. They possess the knowledge to detect problems accurately and carry out repair work efficiently. Documenting all repair service activities and parts replacements is critical for keeping an extensive maintenance background, which can aid in future troubleshooting.
Finally, executing a positive method, including regular assessments and predictive maintenance strategies, improves the integrity of product packaging machines. By adhering to these ideal methods, organizations can make certain optimal maker performance, minimize functional risks, and extend tools lifespan.
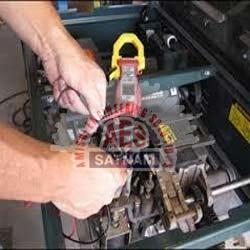
Conclusion
Finally, a comprehensive understanding of product packaging machine elements and efficient maintenance techniques is essential for optimal performance. Normal inspections and the usage of OEM components can considerably decrease downtime, while a well-documented maintenance background fosters positive treatment. Using qualified specialists additionally boosts fixing high quality and integrity. By applying these techniques, organizations can guarantee the durability and effectiveness of product packaging devices, ultimately contributing to enhanced functional performance and minimized costs.
Reliable maintenance of packaging machines hinges on an extensive understanding of their essential components, including the frame, drive system, and securing devices.Efficient operation of packaging makers counts greatly on regular maintenance to prevent typical problems that can interrupt production.Executing preventative upkeep techniques is vital for maintaining the performance and dependability of product packaging makers. Furthermore, preserving accurate documents of maintenance tasks help in tracking the machine's efficiency over time, helping with informed decision-making pertaining to future maintenance needs.
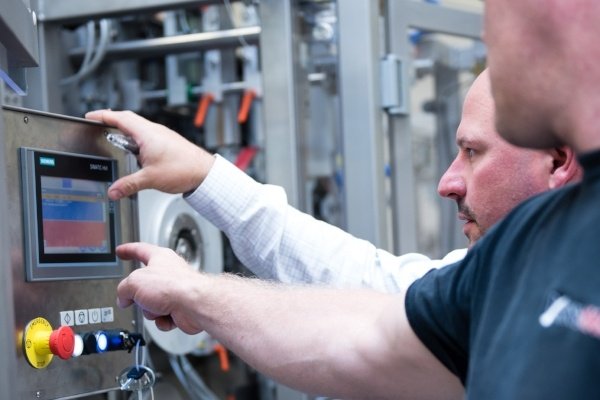